Structural Mechanics
Different load phenomena on mechanical structures can be investigated and analyzed using the Finite Element Method (FEM). Nowadays, its application is an essential instrument in the construction and design of machines and components. B&B-AGEMA uses modern, commercial FEM software and relevant tools to provide the following engineering services:
- Structural analysis
- Thermomechanical analysis
- Vibrational analysis
Structural analysis:
General investigation and analysis of mechanical stresses within a structure under external loads and pressures is an essential task in the engineering process of machines and structural elements.
By the application of appropriate software tools, B&B-AGEMA solves such issues on many different scales of complexity - from simple, linear-elastic calculations to complex, transient and non-linear interactions.
In addition, based on these FE results, subsequent analysis can be performed, like fatigue analysis and lifetime assessments.
Application Examples:
- Linear-elastic structural assement of turbomachinery blading under rotational load
- Non-linear plastification calculation of fir-tree grooves in a rotor shaft and subsequent strain-based lifetime calculation
- Analysis of frictional contacts between components (e.g. root and shroud contacts of bladings)
- Stress analysis of gas valve bodies, including bolted flanges and coverplate
- Dimensioning of coupling bolts and locking pins under consideration of frictional contacts
Thermomechanical analysis:
Stresses in a component may not only be caused by external loads, but also be thermally induced. Heating or cooling of mechanical components can cause dissimilar thermal expansion due to temperature gradients or - if more than one material is being used - different thermal expansion rates. This in turn generates internal stresses or can exert loads on components that are in contact with each other.
To predict those thermal stresses, the knowledge of the temperature field within the component is crucial and it can be calculated by our engineers for stationary as well as transient heating scenarios with FE methods.
If the temperature field is determined by convective effects, B&B-AGEMA can couple CFD or Conjugate Heat Transfer (CHT) methods to accurately predict the convective heat transfer.
Subsequent analyses, like low-cycle fatigue calculations for thick-walled components can be carried out as well.
This enables the identification of critical thermally-induced stresses and thus allows to adapt the component design in order to prevent possible material fatigue or damage.
Application Examples:
- Transient thermal shock analysis of steam converter valves and desuperheaters with subsequent lifetime assessment
- Analysis of thermally induced stresses and strains in watercooled grate segments of a grate firing
- Evaluation of a boiler's superheater steam manifold under restricted thermal expansion
Turbine Exhaust Gas Burner Windbox
- Transient FE analysis for determination of principal stress range
- Thermal boundary conditions determined with CFD simulations
- Low-Cycle Fatigue analysis and lifetime calculation (EN 12952-3 standard) for reference case and subsequent modifications
- Identification of critical locations and improvements in lifetime
- Iteratively, a satisfactory design solution was achieved
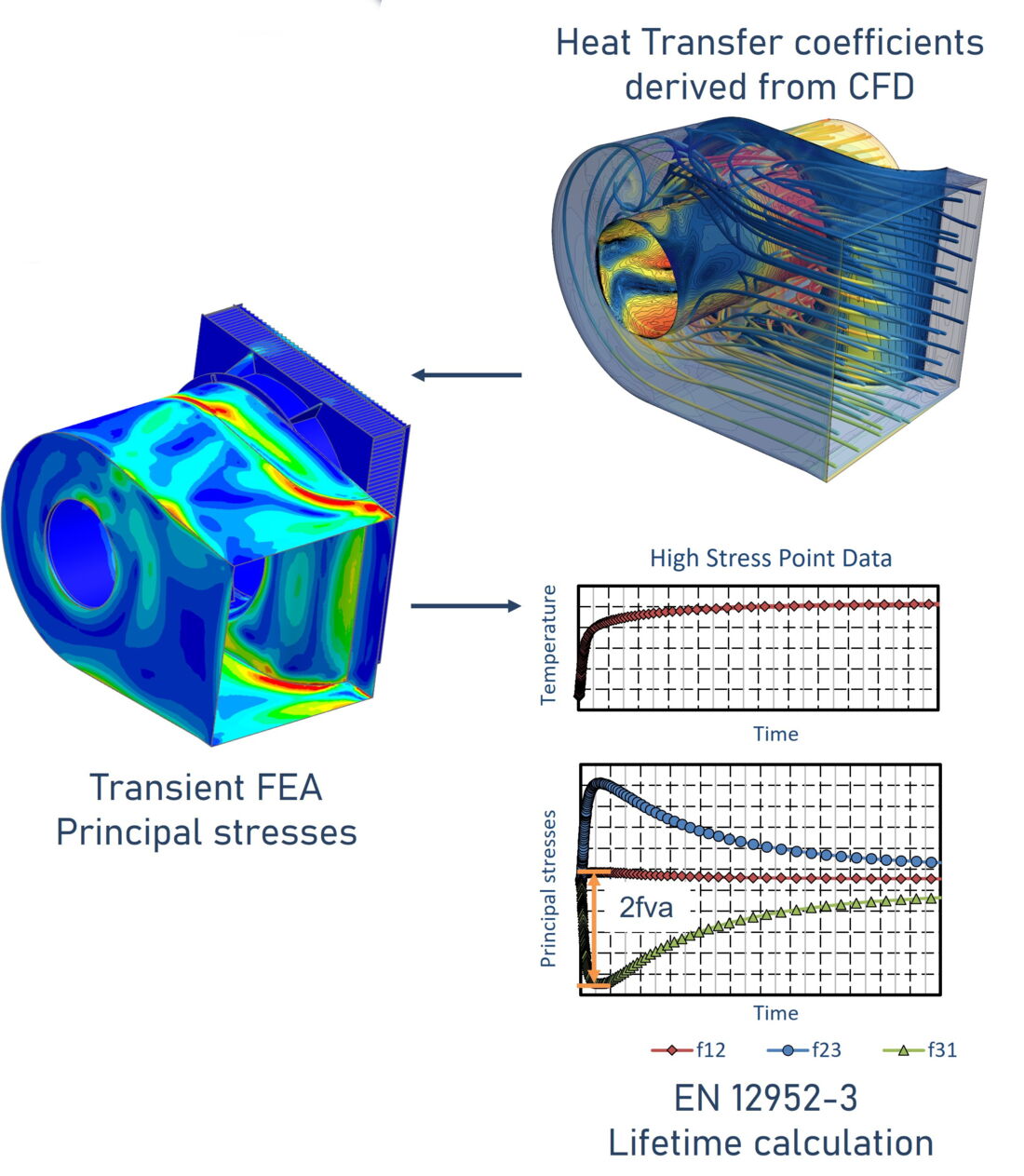
Vibrational analysis:
Another application of FEM is the prediction of the vibrational behaviour of a component.
A modal analysis predicts a structure's natural frequencies or eigenvalues as well as its eigenmodes. A mode shape is the respective deformation state that would occur at a certain natural frequency. Each natural frequency is therefore assigned an eigenmode.
A forced response analysis provides information about the expected behaviour of a component or assembly under dynamic load and is therefore a valuable tool for assessing the interaction of structures under dynamic movement and the resulting stresses and strains. In a subsequent step, a fatigue analysis may be performed as well.
Furthermore, with specialized software B&B-AGEMA can analyze damping effects (e.g. frictional contacts) that limit the amplitude by dissipating vibrational energy.
Knowing the vibrational behaviour and natural frequencies is an essential step to determine whether resonance with known excitation frequencies - and therefore, subsequent damage - can occur. In that case the component can be adapted in order to alter its natural frequencies and avoid the resonance.
Application Examples:
- Assessment of natural frequencies for shrouded blading, including frictional shroud contact
- High-Cycle fatigue analysis of turbine blade based on forced response analysis with excitation force derived from CFD
- Modal analysis of steam converter valve
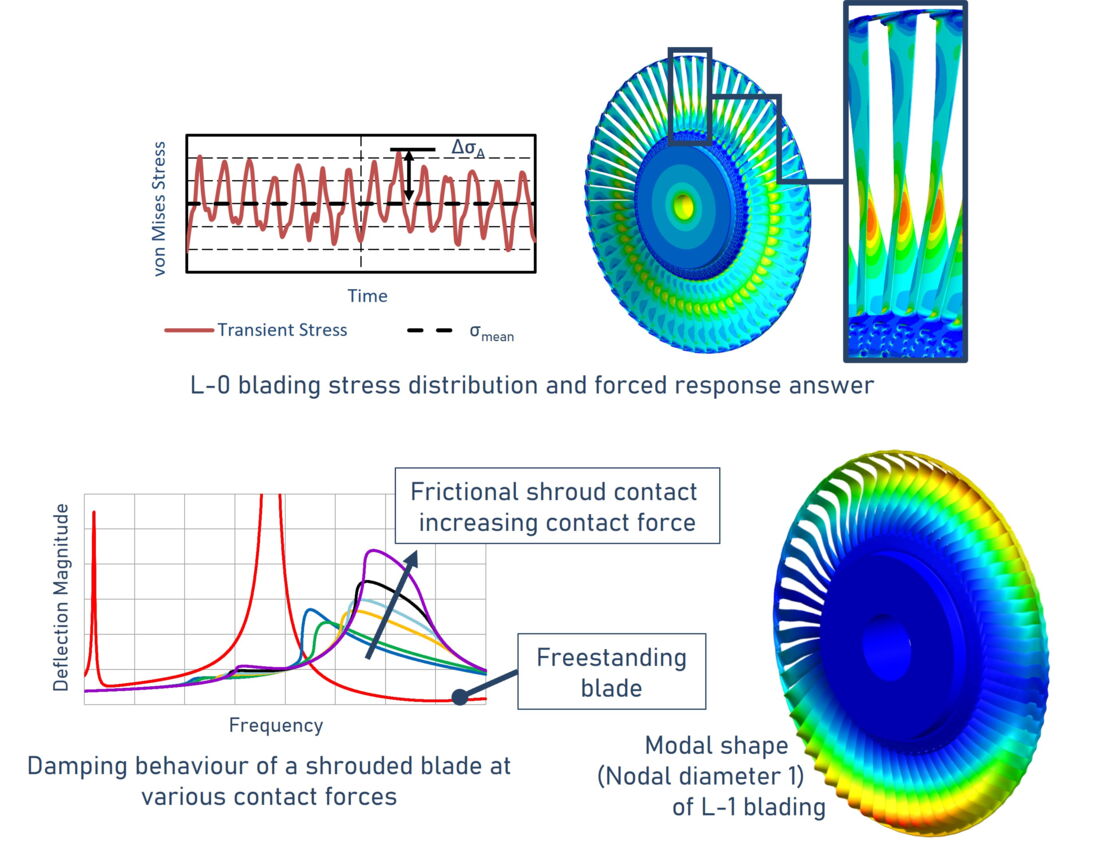
Mechanical design of LP steam turbine blading
- Structural integrity analysis and optimization of blading for all stages
- Static analysis
- High-Cycle fatigue assessment - transient forced response simulation
- dynamic excitation derived from CFD
- Vibrational analysis
- Modal analysis of blading
- Damping optimization of shroud contacts