Steam Turbine
B&B-AGEMA provides core competence for the advanced design and retrofit design of steam turbines and adjoining systems with respect to highest efficiency, availability and reliability. Such work examples include:
- Optimized steam turbine design for industrial and power plant applications
- Modern flow path design including advanced sealing technologies: aerodynamic optimization of blades (3D airfoil design), steam admission chambers, exhaust diffusors, pipes and valves
- Comprehensive structural and aerodynamic modelling of major steam turbine components for accurate life assessment and relative thermal expansion calculations
- Retrofit concepts for increased steam turbine power output, efficiency and lifetime
- Technical feasibility studies on improvement potentials for existing steam turbine systems
- Expert know-how for the analysis, evaluation and improvement of steam condensers, preheaters, reheaters, cooling towers and other steam turbine and power plant components
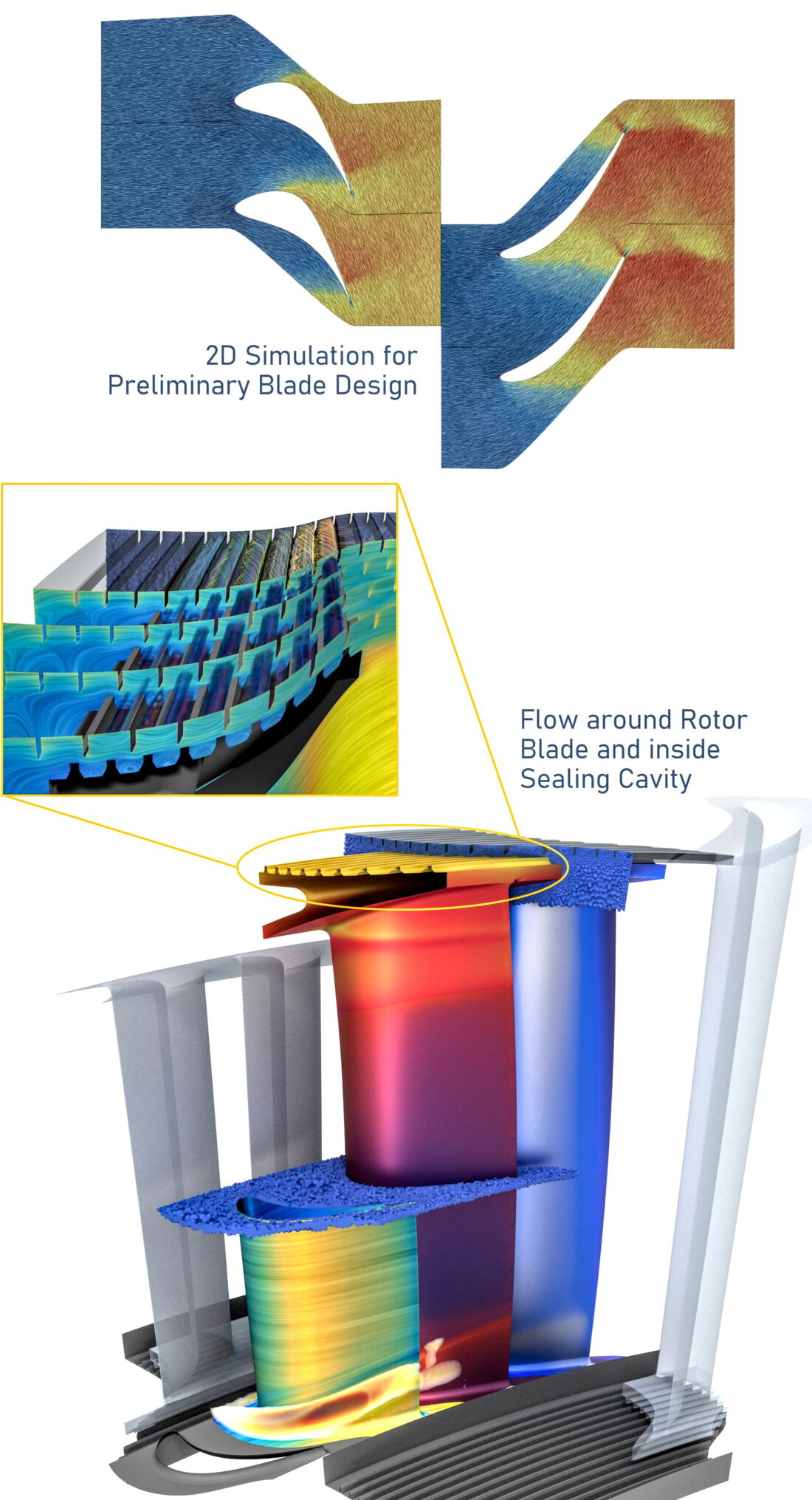
Low Pressure Steam Turbines
Development of Low Pressure Axial Steam Turbines is a challenging field, due to low density and high velocities in the last turbine stages. These result in transsonic flow and large outlet cross sections which pose a challenge to both the aerodynamic and mechanical design. Together with our senior experts a range of new design and refit projects have successfully been completed. A typical development workflow to optimize an existing turbine for better efficiency and higher output power may include the following tasks:
- Inlet housing design based on stationary 3D-CFD
- Development of a sealing concept and its dimensioning
Blade Design:
-
- Thermodynamic modeling of the expansion process and preliminary stage design using ATF1D
- Preliminary blade profile using 2D-CFD
- Blade optimization using stationary 3D-CFD, first stageswise then including all stages
- FEA of rotating blades (static FEM, dynamic HCF-analysis, modal analysis including damping of shroud contacts)
- If needed, adjustments to blade geometry to ensure mechanical integrity
- Diffuser layout for minimum pressure loss and maximum pressure recovery within the geometric limits
- Outlet housing optimization for reduced pressure loss
- Full fidelity 3D CFD including inlet, all stages with sealings, diffusor and outlet to asses the efficiency
Micro Steam Turbine
Apart from engineering and optimizing machines for long proven applications and power outputs, we are always interested in exploring and developing new concepts and ideas. With the need for more efficient processes and a more sustainable use of ressources steam turbines of decreasing power will become economical for producing electrical power. To maximise the efficiency of such small turbines issues like secondary flows and sealing configuration need to be prioritized as they are main causes of aerodynamic losses. The engineers and senior experts here at B&B-AGEMA developed an aerodynamic design for a 250 kWel steam turbine, running at high rotational speed and optimized for high efficiency. To achive this, a similar routine as described for low pressure turbines has been applied, but the boundary conditions for this case lead to differing stage parameters thus leading to a completely different aerodynamic and mechanical blade design as compared to one with higher power output.
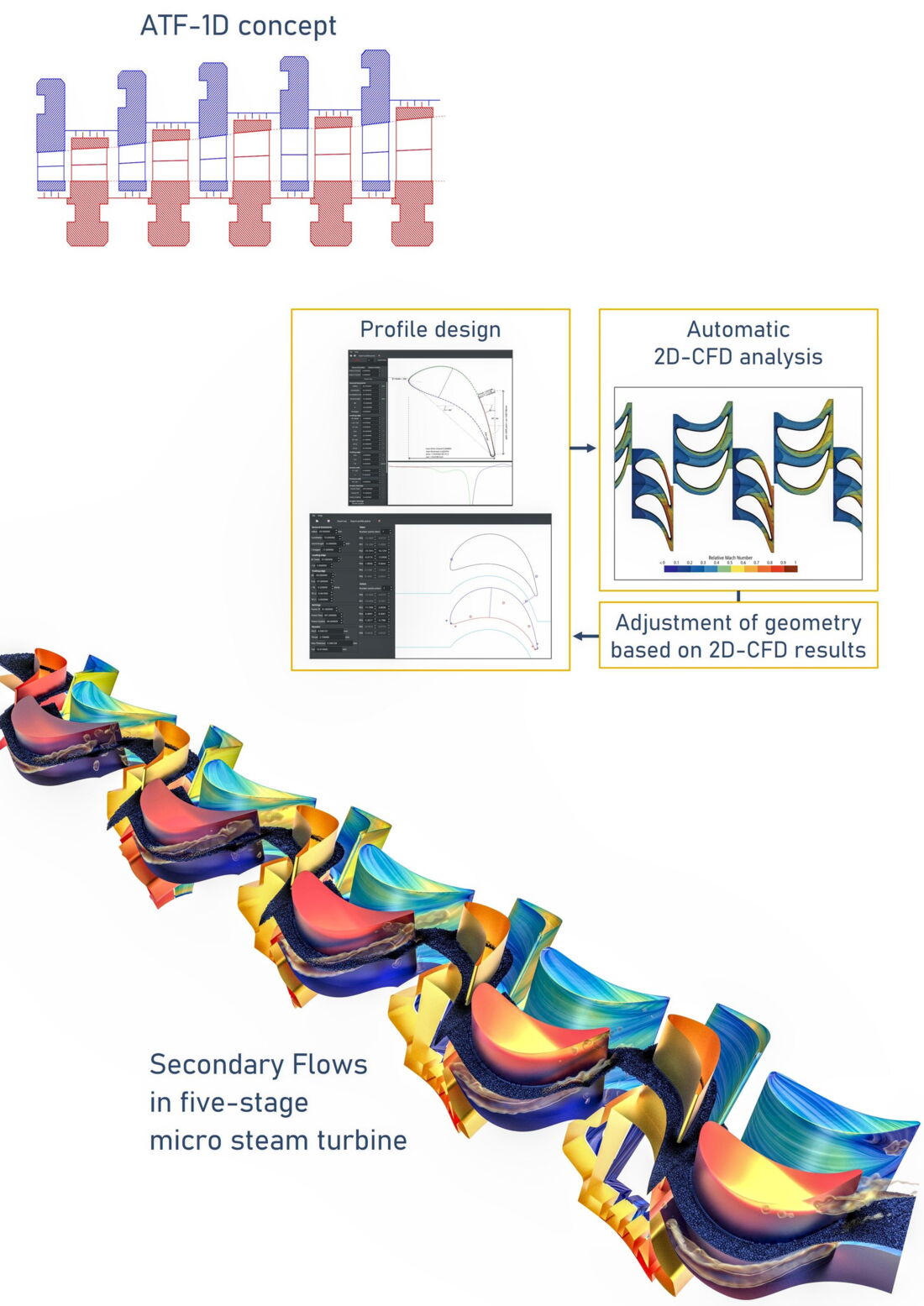
Examples
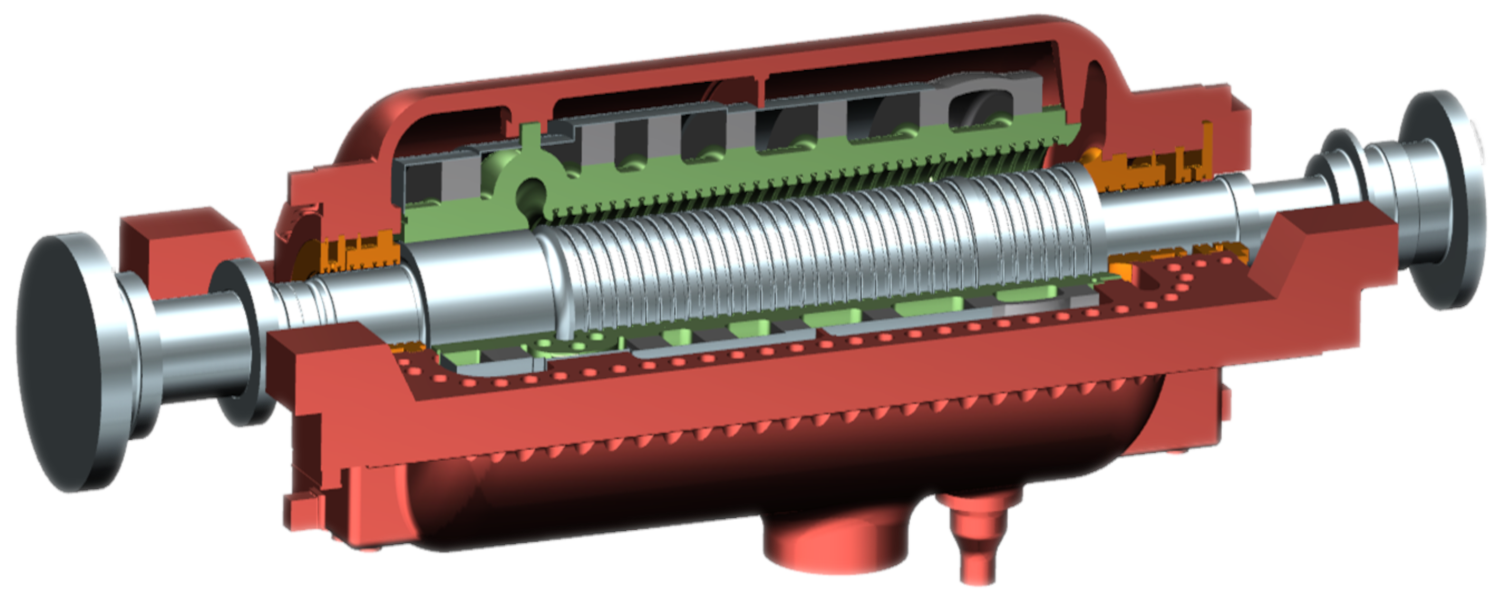
High-Pressure Steam Turbine Design Concept
- 3D aerodynamic design through 3D-CFD
- Layout and dimensioning of sealing configuration
- Mechanical design of rotating parts using FEA (static and dynamic including all mechanical and thermal loads)
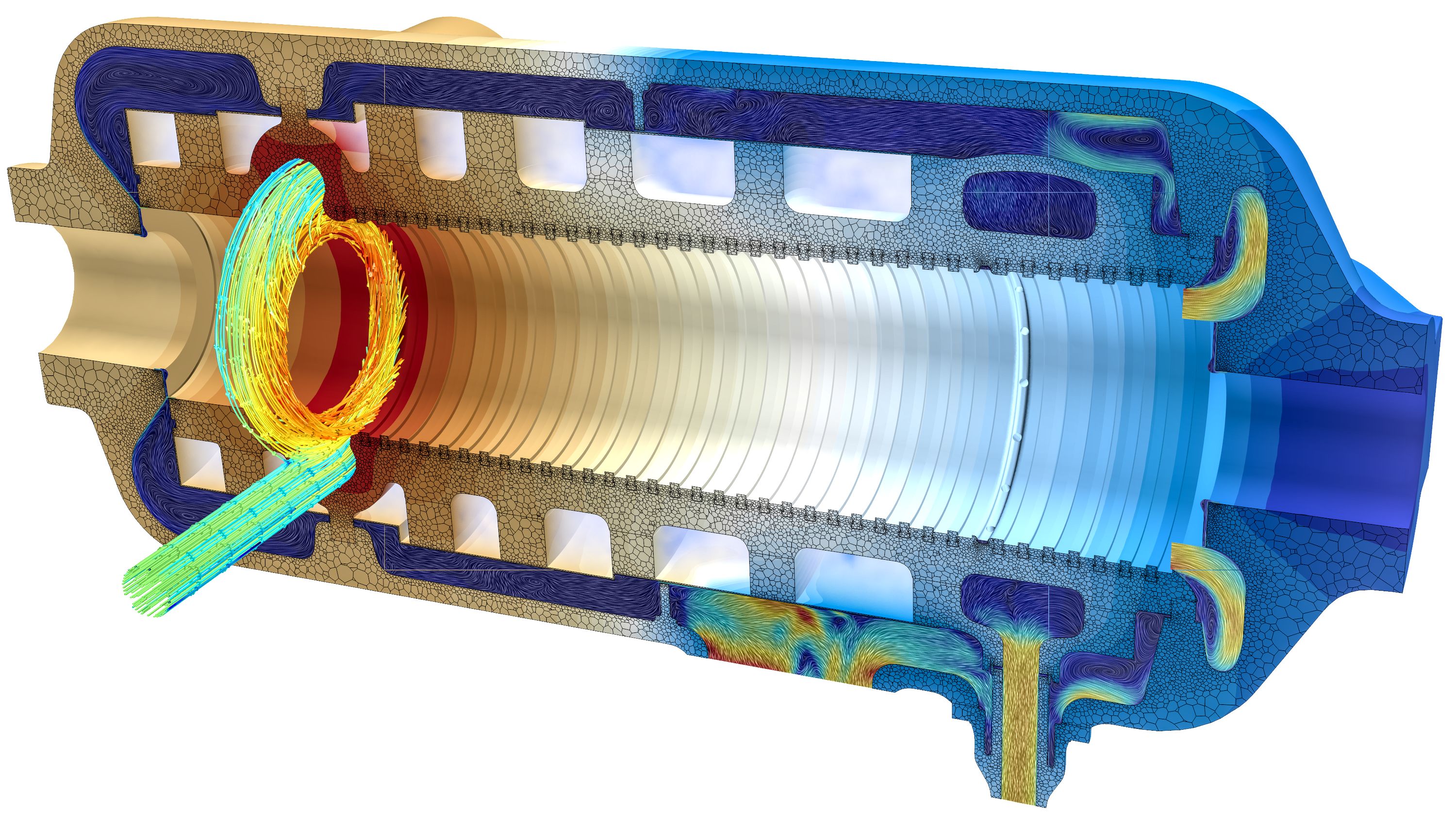
Thermal Analysis of a High-Pressure Steam Turbine
- CHT analysis of high-pressure turbine casing inlet and outlet
- Thermal design and proof of mechanical integrity